A review of the literature on. Bending Coefficient Cb Cb is a moment coefficient to account for the effect of different moment gradients on lateral - torsional buckling Cb 10 for a uniform moment diagram Which represent the worst.
17 Introduction To Cb Bending Coefficient Part 1 For Steel
13 Lateral Torsional Buckling cont Moment Gradient Factor Cb The moment gradient factor Cbaccounts for the variation of moment along the beam length between bracing points.
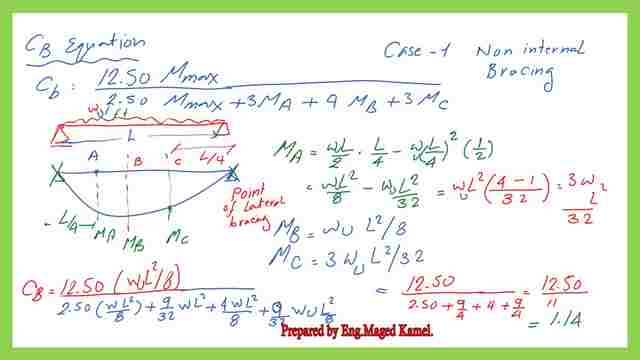
. 3 - Click the Design button to have the module evaluate steel sections from the database according to your criteria. Start with the differential equation giving the deflected shape of an elastic member subjected to bending. Structural Steel shall conform to the requirements of ASTM Designation A283M.
M EI d y d Py. Hot Rolled Steel - Design. Cb Factors are described in Chapter F of the AISC code and are used in the calculation of the nominal.
Our expert stylists will help you shine. A PL 38 x 7 tension member is connected with three 1-inch-diameter bolts as shown in Figure. Lateral-Torsional Buckling Modification Factor.
Welcome to CB Hair Design hair salon locates in KeyportNJ. The 14th edition combines both methods in one volume and provides common requirements for analyses and design and. CB Hair Design 732 947-0255.
ITEM 60926520011 - STEEL FACING FOR CURB ON STRUCTURE NYC TYPE D Jan 2001 USC 11911 Page 1 of 2 DESCRIPTION Under this item the contractor shall supply and install steel facing for curb on structure at the locations indicated on the plans. Steel Design Structural design standards for steel are established by the Manual of Steel Construction published by the American Institute of Steel Construction and uses Allowable Stress Design and Load and Factor Resistance Design. Set equal to zero.
EI d y d Py 0. ASDIP STEEL calculates the Cb factor and finds the unbraced length of each segment along the beam accordingly. 2 - Click the database access button and select from the built-in AISC section database.
Cb in AISC beam design has been calculated using Mmax and three 14 point moments along the unbraced length M A M B and M C. Any conflict between the Guidelines and an applicable code ordinance statute rule regulation andor law shall be addressed. Cb in AISC beam design has been calculated using Mmax and three 14 point moments along the unbraced length M A M B and M C.
This is a link to download the pdf file used for the illustration of this post. Cb 125M max ----- 25M max 3M A 4M B 3M C. Fo r more detailed illustrations for the CB please follow this Flexural Limit State Behavior.
For the next post Cb The coefficient of bending part-2. The Significance and Application of Cb in Beam Design Engineering Journal American Institute of Steel Construction Vol. α2 P EI.
Full code checking member optimization can be applied to standard steel shapes based on the following codes. Bending Coefficient Cb Cb is a moment coefficient to account for the effect of different moment gradients on lateral - torsional buckling Cb 10 for a uniform moment diagram Which represent the worst case of compression flange buckling resulting in the least beam moment resistance In general Cb 125 M max 25 M max 3 M A 4 MB 3 MC M M MA. AISC 360-16 15th Edition ASD LRFD.
Its value is highest Cb1 when the moment diagram is uniform between adjacent bracing points. Divide everything by EI. Use AISC Equation E3-2 or E3-3 and determine the nominal axial compressive strength for the.
Cantilever Flexural Member Design By Sam Eskildsen PE Structural Design Group Birmingham AL Answer Introduction The AISC 1999 Load and Resistance Factor Design Specification for Steel Buildings1 has no specific flexural design requirements for cantilever beams beyond requiring Cb 1 when the free end is unbraced. Ch 4 Section 43 AISC Requirements Exercise 1. The design team shall be responsible for producing designs that comply with the Guidelines in addition to all applicable codes ordinances statutes rules regulations and laws.
CENG 4412 Lecture 13 October 24 2017 Part 2. D y d P EIy 0. CB Hair Design 732 947-0255.
How To Apply a Steel Design Code. With this information and the local buckling properties of the section the shear and bending capacities are calculated for the different limit states. Ch 3 Section 32 Tensile Strength Exercise 1.
Set the variable α2. CB value 125012 4296cb961250 42128125042238. Get 20 off this month when you try our services.
Then plug that in to get. 1 - Simply type the AISC name into the Steel Section Name field and press Tab. Steel beams design is affected by the location of the lateral bracing.
The basic provisions related to design and evaluation of bending members in the structural steel specifications either according to Load and Resistance Factor Design LRFD1 or Allowable Stress Design ASD2. Welcome to CB Hair Design hair salon locates in KeyportNJ.
17 Introduction To Cb Bending Coefficient Part 1 For Steel
17 Introduction To Cb Bending Coefficient Part 1 For Steel
Cb And Lb For Cantilever Column Structural Engineering General Discussion Eng Tips
15 Bending Coefficient Steel Structural Design Prof Shehab Mourad
17 Introduction To Cb Bending Coefficient Part 1 For Steel
15 Bending Coefficient Steel Structural Design Prof Shehab Mourad
Beam Lateral Torsional Buckling Cb Yura Equation Limits Existing Steel Beams Structural Engineering General Discussion Eng Tips
0 comments
Post a Comment